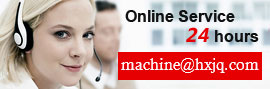
Magnetic separator applied to tailings recycling
In 2005, the concentrator factories adopt high frequency vibrating screen and composite tailings selection technology and flashing magnetic separator. As a result, the ore tailings final grade was reduced by an average of 2.44%. Figures showed that we annually may elect from the tailings 31,190,000 tons of iron ore concentrate, with the concentrate grade 67. 13%, which can achieve annual benefit of RMB 54 million. Production practice of iron ore tailings re-election indicates that ore concentrator factories discharge 2.28 million tons of tailings a year. The tailings processed by the JHC rectangle ring type magnetic separator, and we gained elected rough ore concentrate, and then the concentrator is pumped to a separate built concentrate plant. It will go through weak magnetic separation, grinding-classification, magnetic dewatering tank and double drum weak magnetic separation process, and finally we get the final ore concentrate.
At present, the tailings discharged are about 400million tons to 500 million tons in China, accounting for one third of industrial waste. Among of them, the metal tailing takes for one forth, metallurgy and boiler slag take for 26%, chemical slag takes for 4%, fly ash and gangue take for 35%. The metal recycling process will use magnetic separator and other matched ore dressing equipment. The tailing slag recycling process adopts gravity separation and magnetic separation process, so that recycle iron ore from tailings. As for different metals in the tailings, we will use spiral chute, shaking table and strong magnetic separators with different specifications. For the time being, disk magnetic separator in weak magnetic field, big drum cylindrical magnetic separator in medium magnetic field and high gradient magnetic separator all have been applied to tailing recycling production.
It exist problems in ore magnetic application
1. Because of large amount of lean ore (97.5% per cent of total reserves) and large hardness of the ore materials, magnetic drum cylinder constantly suffers impact of granular iron ore below 0~15mm. So, the wearing is serious, phenomena of magnetic drum blistered is very common. Once the tube mill worn out, ore slurry will pulp into the magnetic drum and attached on the surface of the magnetic system. That will lead to cylinder lock with magnetic system, or cause damage to the bearing, causing the entire equipment destroyed.
2. Magnetic systems generally use strontium ferrite magnets and neodymium-Iron-Boron magnets. Chemical stability of neodymium-Iron-Boron magnets is poor. In humid air inside of magnetic drum, it is susceptible to progressive tiered spalling of oxide on the surface. Chemical stability of strontium ferrite is good, which generally bonded into a magnetic-fixed in the magnetic system with epoxy resin, there are also easily dropping off for magnetic blocks.
Both strontium ferrite magnets are neodymium-Iron-Boron magnets are fixed are necessary.