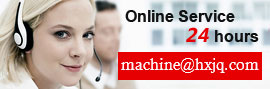
Dust Catcher Has Improved Powder Separation Conditions
As a very important part of the industrial grinding system, the dust catcher has gone through three generations since its birth. The first dust catcher is the centrifugal dust collector which can improve the distribution situation of the materials in the dust collector and improve the dispersibility of the material in the airflow. The second generation dust catcher is the cyclone dust collector which can reduce the circulation of the fine powder with the return air and reduce the concentration of the powder in the powder room. The third generation of the efficient dust catcher produced by Henan Hongxing Mining Machinery Co., Ltd. not only retains the advantages of outer loop of the cyclone dust collector, but also uses the planar spiral airflow beneficiation principle, which has improved the powder conditions fundamentally. The efficient dust catcher is widely used in the raw material mill and the cement mill system in the new generation of the dry process production line.
The new generation of the efficient dust catcher has the following characteristics.
First, the rotor blade with special shape replaces the rotor blade with original shape so that the separation area for the powder increases. In the actual case, the materials have higher separation rate and better separation effect.
Second, the eddy current scattered device inside the rotor can avoid the pressure drop generated by the eddy current or reduce the pressure drop of the dust collector. The eddy current scattered device transfers the energy generated by the rotation of the air stream to the rotor to reduce the power consumption of the drive means and avoid the energy consumption generated by the eddy current. The tangential velocity at the exit of the dust collector can be reduced because of the eddy current scattered device. In addition, the attrition can be also reduced.
Third, the distribution of the finished particles is even and the graduation of the particles is more reasonable.